Laser Welding
Laser Welding Overview
Laser welding is useful in a variety of situations and product applications. One of the best use cases is for welding spring energizers. Through many years in the business, we've found that one of the most common contributors to seal failures is an improper or missing energizer spring weld.
An improper weld can lead to a "high point" on the sealing lip which causes uneven pressure, leading to premature wear and part failure. When a spring weld is missing, the spring cannot provide adequate evenly distributed support, leading to support gaps and possible part failure. Laser welding creates a precise weld, allowing for even distribution of load to ensure proper sealing.
Have questions about this or other services? Ask an MW expert.
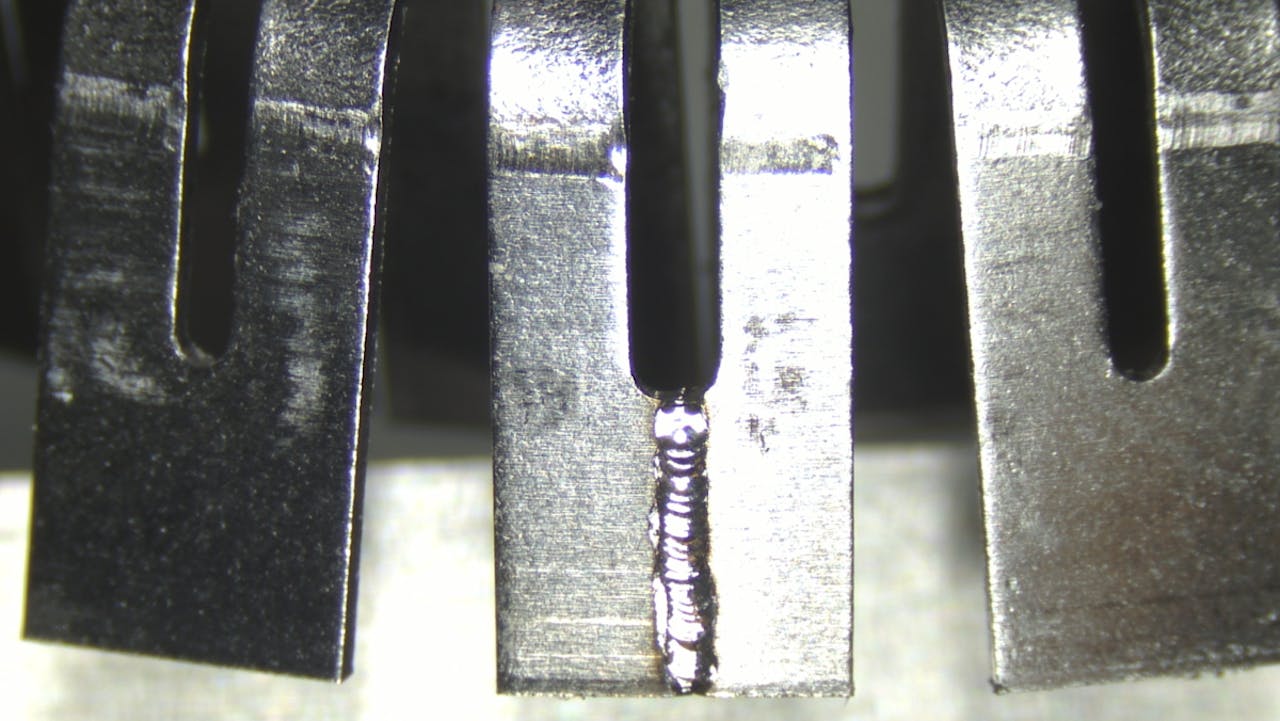
Spring Energizer Weld Configurations
Advantages of Laser Welding
There are several advantages of laser welding, including precise and even weld joints which make it ideal for small components. Some of the many benefits are listed here.
- Precise Welding
- Even Welding
- Efficient
- No Weld Tabs
- Limited Heat Transfer
- Ability to Weld Cross Sections
Applications
Laser welding is recommended for slant coil springs, helical springs, and cantilever springs; however, it can also be used in a variety of other applications.
- Cantilever Springs
- Helical Springs
- Slant Coil Springs
Industries Served
This manufacturing service is applicable to a variety of industries. Some of the industries we work with are listed below.
Ready to Get Started?
Click the button below to request a quote and start your journey with MW.